Given the potentially high dust velocities, the kinetic energy distribution and fluence of the dust particles must inform the instrument design. Since the mass and size distribution is unknown close to the Sun, the design relies on the JHUAPL/UTEP models developed specifically for PSP (Mehoke et al. 2012). The model predicts about 100 impacts from 10- micron particles and 1000 impacts from 0.1-micron particles at the heat shield during the seven years of the mission. It also predicts that most particles will have diameters below 10 microns. Dust impacts can cause increased stray light levels for WISPR in two ways: (1) by damaging the edges of the forward baffles and, (2) by pitting or cratering the surface of the first lens. Additionally, there is an exceedingly small probability (<10−5 for >1 mm particle) of a catastrophic hit by a large particle.
To understand the effects of dust on instrument performance, the WISPR team has undertaken a glass testing and modeling program during the design phase with the help of the German Co-Is (V. Bothmer, PI). The Dust Accelerator at the Max-Planck-Institut für Kernphysik (MPIK) in Heidelberg was used in October 2012 to test three different candidate glass materials for the WISPR optics: BK7, BK7 with a diamond-like coating (DLC), and sapphire. The tests were performed with a variety of iron particle distributions (0.5–3 microns) and speeds (0.5–8 km/s) against three different impact angles (0◦, 45◦, 70◦).
The examination of the impacted glasses showed that sapphire was the most impactresistant material with very small (2 micron diameter; Fig. 11, right) and relatively symmetric craters. The impacts resulted in an unexpected behavior for the diamond-coated BK7. They caused a halo around the impact crater (Fig. 11, middle) that was likely the result of the local detachment of the coating due to the heat produced by the impact. The regular BK7 has relatively small craters (∼5 micron diameter; Fig. 11, left). Overall, the spall diameters are very consistent with the APL/UTEP model and provide confidence in the overall PSP project dust analysis and risk mitigation procedures.
To access the extent of the damaged area we developed an automated software program to measure the size and numbers of craters in the images. The results (see graphic below) show that sapphire is the most robust glass type. However, this type of glass has never been used for space applications before and therefore requires significant development. On the other hand, the standard BK7 suffered only modest damage and it is a well-known material for space options.
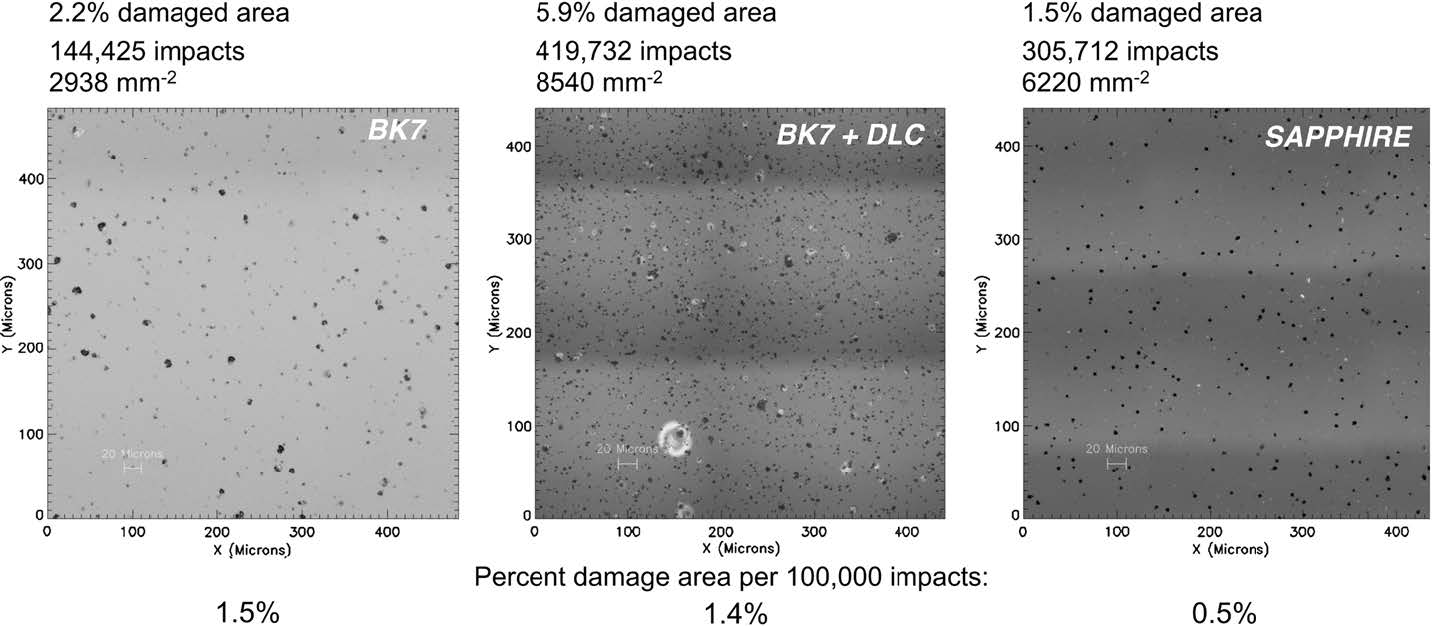
Since the dust testing was in agreement with the APL/UTEP dust model, we use the model to estimate the percentage of damaged area expected for the objective lens of the WISPR outer telescope, which has the most exposure to dust. The model predicts that 0.6 % of the lens area will be pitted by the end of the mission. This value, representing the worstcase scenario, is then adopted for both the inner and outer telescope objective lenses. To evaluate the effect on the imaging performance we first measure the change in the Bidirectional Scattering Distribution Function (BSDF) (or Harvey-Shack function) in the damaged glass relative to the pristine BK7 BSDF. The laboratory-measured BSDFs revealed that we made conservative assumptions in our stray light estimates during the design phase. Therefore, the stray light calculations for pristine and damaged WISPR lenses were rerun using the measured BSDFs. The resulting beginning and end of life optics performances are shown in Fig. 13.
To summarize, the dust testing has been very valuable for the WISPR design process. It validated the APL/UTEP model (for velocities ∼2–3 km/s), allowed to safely reject exotic materials and coatings as an alternative to regular BK7, led to the development of a realistic BSDF model for evaluating the stray light effects of dust impacts on the imaging performance, and provided an estimate on the approximate damaged area of the WISPR optics. Based on these results, the regular BK7 was adopted as the baseline for the WISPR optics.